CONSULTING
Respiratory Protection Program Planning
Respirators are used to protect employees from exposure to hazardoushazardous chemicals or particulate in the air. These can be in the form of gases, vapors, mists, dust, or viral bacteria. If you provide respirators to your employees to protect them from airborne hazards, you must have a written respiratory protection program. The written program must serve as a blueprint for conducting the following at your workplace:
- How the appropriate respirators for particular hazards are selected and issued
- When and how respirators will be used in routine work activities, infrequent activities, and potential emergencies
- How medical evaluations of respirator users are provided
- How respirator fit-testing is managed
- How respirators in use are cleaned, stored, inspected and repaired or discarded
- How sufficiently high-quality air is provided for air-supplied respirators (if applicable)
- How employees are trained about respiratory hazards at your workplace
- How employees are trained on the proper use of the respirators used at your workplace
- How you evaluate the effectiveness of your respiratory program
Get Organized
The answers to the above questions will depend on the site-specific conditions at your workplace. The information must be detailed and reflect actual needs and conditions; not just what seems like the right thing to do. It must describe the actual conditions and operations at your workplace.
To provide proper protection, respirators should be of the right type and must be worn correctly at all times. A routine schedule of maintenance must be maintained. Respirators are prone to failure, relies on the correct behavior of individual employees and may require considerable managerial oversight. For these reasons, PPE is considered a last resort to protect employees in the heirarchy of controls.
It often safer, less hassle, and sometimes cheaper to eliminate or mitigate respiratory hazards through alternate methods such as exhaust ventilation, procedural changes, or isolation of the process. Sometimes the presence of the hazardous material itself can be eliminated. But, when there is no alternative, a respirator program must be implemented to protect your employees from adverse health effects of exposure to airborne hazards.
One Stop Shop
FRONTLINE Fit Testing is your all-in-one solution for Respiratory Protection Program planning. We provide everything from consulting on the requirements of a company respiratory protection plan, to training on respirator use and fit testing. Contact us for more information today!
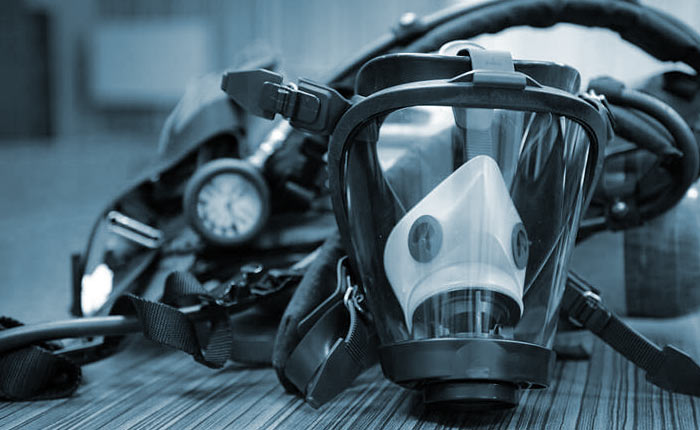